마이크로 LED 전사, 접합, 그리고 불량 화소 수리 기술
MicroLED Transfer, Bonding, and Bad Pixel Repair Technology
- 저자
-
최광성저탄소집적기술창의연구실
엄용성저탄소집적기술창의연구실
문석환저탄소집적기술창의연구실
윤호경저탄소집적기술창의연구실
주지호저탄소집적기술창의연구실
최광문저탄소집적기술창의연구실
- 권호
- 37권 2호 (통권 195)
- 논문구분
- ICT 창의연구, 양자에서 우주까지
- 페이지
- 53-61
- 발행일자
- 2022.04.04
- DOI
- 10.22648/ETRI.2022.J.370206
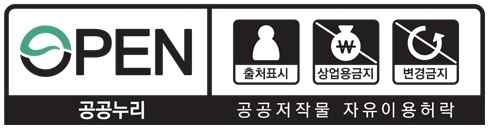
- 초록
- MicroLEDs have various advantages and application areas and are in the spotlight as next-generation displays. Nevertheless, the commercialization of microLEDs is slow because of high cost as well as difficulties in the transfer, bonding, and bad pixel repairing process. In this study, we review the development trends of transfer, bonding, and defective pixel repair technologies, which are critical for microLED commercialization, focusing on materials that determine these technologies. In addition, we focus on the simultaneous transfer bonding technology developed by the Electronics and Telecommunications Research Institute, which has been attracting enormous research attention recently.
Share
Ⅰ. 서론: 마이크로 LED 디스플레이
마이크로 LED(Light Emitting Diode)는 크기가 수십 μm인 LED를 의미한다. 마이크로 LED는 반도체 공정으로 제조되어 무기물로 구현되기 때문에 OLED(Organic Light-Emitting Diode)에 비해 높은 명암비, 빠른 영상구현 속도, 넓은 시야각, 풍부한 색 재현율, 높은 휘도, 저전력, 긴 수명, 높은 신뢰성, 무한한 디스플레이 구현 가능 등의 장점을 보유하고 있다. 이러한 장점으로 인해 마이크로 LED는 TV, 사이니지 등 대형 디스플레이, 노트북, 패드 등 중형 디스플레이, 스마트폰, 스마트워치 등 소형 디스플레이, AR(Augmented Reality)·VR(Virtual Reality)과 같은 마이크로 디스플레이 등 응용 분야가 다양하다. 이에 따라 2027년까지 연평균 65%의 성장률을 기록하며 관련 시장은 710억 달러 규모로 예측되고 있다[1]. 이와 같은 상황으로 인해 LCD(Liquid Crystal Display)에 이어 OLED에서도 디스플레이 종주국으로 대접받는 대한민국의 위상에 도전하기 위해 대만, 중국, 일본, 미국, 유럽이 마이크로 LED 분야 핵심 기술 개발에 총력을 다하고 있다.
마이크로 LED 제조 공정은 반도체 공법으로 사파이어 웨이퍼상에서 마이크로 LED를 제조하는 것으로 시작한다. 제조된 마이크로 LED를 개별 LED로 분리한 이후 디스플레이 패널 기판으로 옮겨 (전사) 심는 (접합) 공정을 수행한 이후에 불량 화소를 수리한 다음 이미지를 구현한다. 중간 테스트 과정을 거쳐 양품의 마이크로 LED만이 디스플레이 화소로 구성될 수 있도록 한다.
마이크로 LED는 많은 장점이 있지만, 아직 상용화에 성공했다고 할 수 없다. 그것은 너무나도 비싼 가격 때문이다[2]. 이와 같은 비싼 가격의 원인은 첫 번째 마이크로 LED 자체의 가격이 비싸기 때문이다. 이 문제를 해결하기 위해 디스플레이 제조 회사들은 마이크로 LED 크기를 줄이면서도 휘도를 유지하는 기술 개발에 힘쓰고 있다. 한 번의 반도체 공정으로 더 많은 마이크로 LED를 생산함으로써 생산 단가를 줄이려는 전략이다. 두 번째는 옮겨 심는, 다시 말해 전사와 접합 공정비용을 줄이는 기술 개발에 총력을 다하고 있다.
예를 들어, 8K 디스플레이는 마이크로 LED 수가 약 1억 개 정도 된다. 이것의 전통적인 방법은 Pick and Place 공법으로, 전사 접합하면 약 11년이 걸린다고 한다[3]. 불량 요인은 마이크로 LED 자체의 품질 문제, 전사 및 접합 공정의 문제 등으로 인해 상존한다. 8K 디스플레이에서 99.99%의 수율을 가정하면 약 1만 개의 불량 화소가 발생하며 임의의 화소에서 발생한 마이크로 LED를 1개씩 수리하고, 그 수리 시간이 5분의 시간이 걸린다고 하면 총 5만 분, 다시 말해 약 한 달의 시간이 소요되므로 불량 화소 수리 시간을 줄이는 것이 매우 중요하다. 욜 디벨롭먼트는 2021 SID에서 마이크로 LED 디스플레이 상용화, 즉 저가격화를 위한 요인과 효과를 다음 4가지로 분류하였다[4].
1) 마이크로 LED 크기 축소
2) 수율 향상과 불량 화소 수리 공정 효율화
3) 전사 및 접합 공정의 생산성 증대 및 관련 공정의 비용 감축
4) 양산 효율 증대
상기에서 각각의 효과를 분석한 결과 1)은 4~70배, 2)는 1~50배, 3)은 8~120배, 4)는 1.5~2배에 이른다고 하였다.
이 분석 결과를 보면 마이크로 LED 자체의 가격을 낮추는 것보다 전사, 접합 공정의 생산성 증대 및 비용 감축과 수율 향상 및 불량 화소 수리 공정 효율화가 더 효과적임을 알 수 있다. 대한민국이 강점을 가진 양산 효율 증대 부분은 효과가 미비한 수준이다. 이것이 의미하는 것은 아직 산업계가 받아들일 만한 생산성과 안정성, 그리고 신뢰성을 가진 전사, 접합, 그리고 불량 화소 수리 공법이 개발되지 않았다고 받아들일 수 있다.
본고에서는 마이크로 LED의 상용화에 있어 가장 중요하지만, 지금까지 해답을 찾지 못하고 있는 전사, 접합, 그리고 불량 화소 수리 기술 개발 현황에 대해 논하고자 한다. 먼저 전사, 접합에 사용되는 소재를 살펴본 이후 공정에 대해 논의할 예정이다. 이는 소재가 공정을 결정하는 가장 핵심 요인이기 때문이다.
Ⅱ. 본론: 마이크로 LED 전사, 접합, 불량 화소 수리 기술
1. 소재 기술 개발 동향
전통적으로 디스플레이에서 사용됐던 접합 소재는 ACF(Anisotropic Conductive Film)이다. 이것은 일본의 쇼와 덴코사(구, 히타치 화학)가 원천기술을 가지고 있다. ACF는 전도성 볼이 필름에 균일하게 분포되어 있고, 접합 공정 이후 그중 일부의 볼이 상하 전극 사이에 존재하게 되어 상하 전극 사이의 전류가 흐르도록 한다. 이때 전도성 볼의 간격은 넓어서 평면상으로 다시 말해 인접한 볼 간에 전류는 흐르지 않는다. 최근에는 마이크로 LED가 워낙 작아서 전도성 볼을 필름 내에 균일하게 분포시키는 대신 접합 후 전극 위치 부분에만 전도성 볼이 분포하도록 전도성 볼의 위치를 인위적으로 설계한 제품이 나오고 있다.
ACF는 전극 중 일부분만 수직 전류 흐름에 사용된다. 이로 인해 그림 1에 나타난 바와 같이 전극 전면을 수직 전류 흐름에 사용하는 솔더를 기반으로 하는 접합 기법에 비해 접촉 저항이 수십 혹은 백 배 이상 크다[5]. LCD나 OLED는 각각 전압 구동 혹은 낮은 전류로 구동하기 때문에 접촉 저항에 큰 영향을 받지 않으나 마이크로 LED의 경우 전류가 크기 때문에 문제가 발생할 수 있다. 더욱이 마이크로 LED 동작 중에 발열이 되기 때문에 열 전도성이 0.5W/m·K 이하인 ACF는 적절하다고 생각하기 어렵다. 이에 반해 솔더는 열 전도성이 조성에 따라 수십W/m·K 정도여서 상대적으로 열을 쉽게 제거할 수 있다는 장점이 있다. ACF는 필름을 주로 구성하는 경화된 고분자의 접착력에 의존하므로 금속 간 화합물에 기반을 둔 솔더 접합에 비해 접착력이 떨어지고 장기 신뢰성이 낮아질 우려가 크다. 여기에 흡습 신뢰성 시 고분자 필름이 수분을 흡수하여 부풀어 올라 접합 신뢰성이 떨어지는 경우도 발생한다. 마지막으로 ACF는 열 압착 공정을 통해 접합 공정에 적용된다. 이때 고분자가 경화되어 전기전도성과 신뢰성을 보장할 수 있게 된다. 이로 인해 불량 화소 수리 공정이 어렵게 되는 단점이 있다. ACF를 적용하여 마이크로 LED를 디스플레이 패널 기판에 접합한 경우 이를 제거하려면 기계적으로 제거할 수밖에 없고 자연스럽게 불량 화소 수리 공정의 비용과 시간을 증가시키는 요인이 된다.
솔더를 이용하는 접합은 전통적으로 전자 패키징에서 자주 사용되어오던 기법이다. 플립 칩 본딩 기법에서 플럭스와 언더필을 이용해서 접합 공정을 수행해왔다[6]. 플럭스와 언더필은 모두 일본에서 처음 개발했으며 지금도 첨단 제품에는 모두 일본 기업 제품이 적용되는 편이다. 이 공정은 플럭스 도포 → Pick & Place → 리플로우 → 플럭스 잔사 세척 → 기판 습기 제거 → 플라즈마 처리 → 언더필 도포 → 언더필 경화의 8단계 이상으로 구성된다. 이 공정은 마이크로 LED에 적용하기 어려운데 접합 공정 후 마이크로 LED와 기판 사이의 거리 즉, 접합부의 두께가 너무 얇기 때문에 플럭스 잔사 세척, 언더필 도포 등의 공정이 불가능하기 때문이다. 마이크로 LED처럼 금속 전극의 간격이 너무 작으면 리플로우 공정 중에 마이크로 LED가 움직임으로 불량이 발생할 가능성이 너무 커서 적용하기가 어렵다는 점도 있다.
이러한단점을극복하기위해 NCP(Non-Conductive Paste)와 NCF(Non-Conductive Film) 소재가 개발되었다[6]. 이 소재도 일본의 쇼와 덴코사가 세계 최초로 개발하여 HBM(High Bandwidth Memory) 생산에 적용되고 있다. 마이크로 LED용으로는 부피를 제어하기 쉬운 NCF가 좋다. NCF는 솔더의 산화막 제거 기능과 언더필 기능이 하나의 필름으로 구현되어 있어 앞서 언급한 플럭스와 언더필의 단점을 극복할 수 있다. 그렇지만, 일정 부분 흄이 나오는 것과 그림 2와 같이 열 압착 공정을 하면 NCF를 이루는 고분자가 경화되어 불량 화소 수리가 어렵다는 단점은 ACF와 동일하다. 열 압착 공정에서도 NCF는 ACF와는 다르다. ACF는 일정한 온도의 Heater Block이 사용되지만, NCF에 적용되는 세라믹 히터는 100℃에서 250℃ 혹은 300℃ 사이를 NCF 소재에 적합한 일정한 온도 프로파일로 반복해야 한다. 이는 높은 온도에서 NCF의 물성이 변할 뿐만 아니라 솔더 접합을 위해서 NCF를 활성화하는 단계가 필요하기 때문이다. 쇼와 덴코는 NCF를 약 300초 이상의 열 압착 공정을 통해 전사와 접합 공정을 시도하였으나 마이크로 LED 점등에는 실패했다[7].
한국전자통신연구원은 17년간의 연구개발 끝에 SITRAB(Simultaneous Transfer and Bonding) 접착제를 개발하였다[6,8-10]. 앞서 소개한 모든 소재가 일본에 원천기술이 있음에 반해 이 소재는 한국전자통신연구원에 원천기술이 있다. SITRAB 접착제는 페이스트 형태와 필름 형태가 있다. 페이스트 형태는 크기가 큰 미니 LED, 필름은 마이크로 LED에 적합하다(그림 3).
SITRAB 접착제는 모든 구성 성분이 고분자여서 앞서 언급된 NCF와는 달리 흄이 발생하지 않는다. 특히 0.75~5초 범위에서 조사되는 면 레이저의 짧은 시간에 활성화되고 접합이 수행되기 때문에 흄 발생으로 인한 부작용이 발생하지 않는다. NCP/NCF처럼 솔더의 산화막 제거와 언더필 성능을 하나로 합친 소재이다. 면 레이저 조사에도 불구하고 물성이 변하지 않아 반복적으로 접합 공정을 수행할 수 있다는 점은 앞서 소개한 ACF 혹은 NCF로는 구현이 불가능한 특성이다. 한국전자통신연구원은 5 × 5 마이크로 LED 배열을 SITRAB 접착제를 사용하여 점등하였다[6,8]. 여기에 마이크로 LED 배열보다 훨씬 큰 면적에 면 레이저가 조사하였다. 그 후 인접한 영역에 두 번째 5 × 5 마이크로 LED 배열을 점등하였다. 이때 새로운 마이크로 LED가 점등된 SITRAB 접착제는 면 레이저를 2회 맞았다. 최대 5회까지 면 레이저를 조사해도 마이크로 LED가 정상적으로 점등됨을 확인하였다. 이와 같은 SITRAB 접착제의 특성은 불량 화소 수리 비용과 공정 시간을 대폭 줄이는 장점을 제공한다. 이 특성은 타일링 공정, 즉 작은 면적의 공정을 연이어 인접 영역으로 반복하여 대면적을 구현하는 공정을 가능하게 한다. 타일링 공정은 장비 비용을 획기적으로 줄일 수 있는 장점을 제공한다. 이와 같은 장점은 ACF나 NCF에서는 확보하기 어렵다. SITRAB 접착제는 접합 공정과 불량 화소 수리 공정이 완료된 이후 후경화 공정을 통해 최종적으로 경화된다.
2. 공정 기술 개발 동향
전사와 접합 그리고 불량 화소 수리 비용을 줄이기 위해 많은 기술이 제안되었다. 그런데 대부분은 전사와 접합에 대한 것이고 불량 화소 수리에 대한 것은 상대적으로 적은 편이다. 전사 공정을 살펴보면 (1) 일레스토머(Elastomeric) 스탬프, (2) 정전기 MEMS, (3) 레이저 전사, (4) 자가 정렬(Self-assembly), (4) 진공 멤브레인, (5) 미세변위 멤브레인, (6) 광학 핀셋(Optical Tweezer) 등이 있다[3].
이중 상용화에 가장 가까운 일레스토머 스탬프 기법을 그림 4에서 보여준다. 일레스토머 스탬프는 유리와 PDMS(Polydimethylsiloxane)로 구성되어 있고, 여러 가지 공정 변수 및 소재 설계를 통해 점착력을 제어할 수 있다. 다만 대면적으로 확대하기 어려운 것이 단점이다. 인터포저 역시 유리와 PDMS로 구성되어 있다. 인터포저 위에 배열되어 있는 RGB 마이크로 LED는 Laser Lift-Off(LLO) 공정으로 캐리어를 만든 이후 한 번의 전사 공정을 통해 제작한다[11]. 인터포저에서 스탬프의 전사는 점착력의 차이로 이루어진다. 즉, 스탬프와 마이크로 LED 간의 점착력이 인터포저와 마이크로 LED 간의 그것보다 크다. 이어서 스탬프에서 디스플레이 패널 기판으로의 전사도 점착력의 차이에 의존한다. 이때 적용되는 접합 소재가 앞서 언급한 ACF, 혹은 NCF이다. 이들 소재의 점착력을 조절할 수 있는 소재 설계 및 공정 설계 기술이 매우 중요하다.
스탬프를 이용한 전사는 스탬프 면적도 넓게 하기 어렵고, 공정 시간도 한 사이클에 30초 가까운 시간이 걸려서 생산성이 떨어진다[12]. 이에 따라 12억 원을 호가하는 전사 장비에 대한 투자비 규모가 늘어난다. 마이크로 LED의 두께나 표면 상태도 상이해서 전사 수율을 높이기가 쉽지 않다. 여기에 ACF 접합을 위한 압력이 매우 높아 장비 유지 관리가 어려울 뿐만 아니라 마이크로 LED 높이 차이로 인해 압력이 균일하지 않아 취성이 높은 마이크로 LED가 깨지기도 하는 등 다양한 불량 요인이 있다.
이 문제를 해결하기 위해 쇼와 덴코사는 스탬프를 제거하고 인터포저를 바로 열 압착으로 동시 전사 접합하는 공정을 발표하였다[7]. 앞서 소개한 쇼와 덴코사가 개발한 NCF를 적용하였다. 문제는 세라믹 히터로 인터포저를 잡는 순간부터 발생한다. 인터포저를 구성하는 폴리머는 열팽창 계수가 매우 크다. 여기에 세라믹 히터의 온도가 100℃에서 250℃로 상승하면 그 온도로 인해 폴리머가 열 팽창하게 되고 이로 인해 정렬 자체가 틀어지게 된다. 그 결과 쇼와 덴코사는 전사가 완벽하게 이루어진 것으로 발표했지만 정작 마이크로 LED가 점등된 결과는 보여주지 못했다.
한국전자통신연구원은 앞서 언급한 SITRAB 접착제를 기반으로 세계 최초로 마이크로 LED 동시 전사 접합 공정(SITRAB 공정)을 개발하였다 [6,8-10]. 그림 5에 보인 바와 같이 먼저 디스플레이 패널 기판에 SITRAB 접착제를 도포한다. 크기가 큰 미니 LED일 때 SITRAB 페이스트를 스크린 프린팅 공정으로 도포하고 크기가 작은 마이크로 LED일 경우에는 SITRAB 필름을 라미네이션 공정을 통해 패널 기판에 흡착시킨다. 그 이후 마이크로 LED가 배열된 인터포저와 패널 기판을 정렬시킨다. 이때 인터포저는 장비에 있는 쿼츠로 잡는다. 그후 쿼츠를 이용하여 인터포저를 패널 기판에 접촉시키고 압력을 가한다. 면 레이저를 수 초간 조사한다. 다음으로 인터포저를 분리한다.
이와 같은 공정을 가능하게 하는 것은 한국전자통신연구원이 Laser-Assisted Bonding(LAB)에 적합한 소재 기술을 개발했기 때문이다[13-19]. 사용되는 면 레이저의 파장은 980nm이다. 이 대역에서 쿼츠와 인터포저의 흡수율은 매우 낮다. 즉, 인터포저 등이 레이저를 흡수해서 온도가 상승하지 않는다는 것이다. 이러한 현상은 앞서 언급한 ACF 혹은 NCF 기반 열 압착 공정에서는 불가능하다. 다시 말해 인터포저상 마이크로 LED가 열로 인해 위치가 틀어지는 현상이 SITRAB 공정에서는 발생하지 않는다는 것이다.
면 레이저가 조사되면 이로 인해 SITRAB 필름이 활성화되고 솔더 표면의 산화막을 제거한다. 솔더 표면의 산화막은 반드시 제거해야 안정적인 금속결합, 즉 금속간화합물 형성이 가능하다. 1초 미만에서 5초 이내의 짧은 레이저 조사에도 불구하고 산화막이 효과적으로 제거된다는 것과 동시에 흄이 발생하지 않는다는 것이 SITRAB 소재와 공정의 장점이다. 이로 인해 생산성이 향상될 수 있는 것이다. 산화막이 제거되고 열로 인해 금속간화합물이 형성되면 마이크로 LED와 디스플레이 패널 기판 사이의 접합력은 마이크로 LED와 인터포저 사이의 판데르 발스 힘에 의한 점착력보다 매우 크다. 이로 인해 분리 공정을 통해 자연스럽게 전사 공정이 일어나는 것이다. 이것은 그동안의 접근 방법과는 상반되는 것이다. 즉, 전사 공정 이후에 다시 말해 마이크로 LED를 디스플레이 패널 기판에 옮겨 놓은 후 접합하는 기존 방식과는 반대로 먼저 접합을 수행한 이후 인터포저에서 디스플레이 패널 기판으로 옮기는 것이다. 일종의 와해 기술이라고 할 수 있다.
SITRAB 기술의 또 하나의 장점은 다양한 솔더를 사용할 수 있다는 것이다. 한국전자통신연구원은 디스플레이 패널 기판상의 솔더를 SnAg뿐만 아니라 SnBi, In과 같은 솔더를 적용하여 점등하였다[6,8-10]. 이것은 기존의 업체들과는 차별화된 요인 중 하나이다.
면 레이저를 조사해도 물성이 변하지 않는 SITRAB 접착제의 특성을 이용한 것이 그림 6에 나와 있다. 그동안은 인터포저, 즉 RGB 세 개의 LED가 배열된 인터포저가 꼭 필요했다. SITRAB 기술을 이용하면 단일 색의 LED 배열만이 있는 캐리어만을 가지고도 RGB 디스플레이 구현이 가능하다. 먼저 RED 마이크로 LED로 SITRAB 공정을 하고 Green 마이크로 LED로 두 번째 SITRAB 공정을 하고 마지막으로 Blue 마이크로 LED로 세 번째 SITRAB 공정을 함으로 디스플레이를 완성하는 것이다[10]. 어느 색의 마이크로 LED를 사용할지 순서는 상관이 없다. 이로써 인터포저를 만드는 비용과 시간을 절약할 수 있다. 그림 7은 이와 같은 방법을 적용하여 제작한 유연 디스플레이의 64 × 64 칼라 이미지를 보여준다.
불량 화소 수리 공정은 접합 공정에 사용된 소재가 결정한다. 앞서 소개한 ACF, NCF 모두 접합 공정 중에 고분자가 완전히 경화됨으로 인해 불량 화소 수리 기술을 발전시키기가 어렵다. 유일한 방법은 이들 소재를 기계적으로 제거하는 것으로 이로 인해 많은 제거된 필름 조각들이 발생하므로 세척 등의 추가 공정이 필요하다.
그림 8은 SITRAB 기술을 활용한 불량 화소 수리 공정을 보여준다. 핵심은 하나의 픽셀 안에 RGB 여유 전극을 각각 형성하는 것이다. 즉, 총 6개의 마이크로 LED용 전극이 하나의 픽셀 안에 있는 것이다. 실제로 마이크로 LED는 이 중 3개의 전극에만 접합되어 있다. 테스트 후에 예를 들어 Blue 마이크로 LED가 불량으로 판정되면 레이저 등을 이용하여 마이크로 LED 혹은 이에 연결된 전극을 파괴한다. 그 이후 새로운 Blue 마이크로 LED를 적용하여 SITRAB 공정을 여유 전극 위에서 실시한다. 이와 같은 공정은 모두 그림 6에 있는 바와 같이 면 레이저 조사로 인해 SITRAB 접착제의 물성이 변하지 않는다는 장점에 기초하고 있다.
Ⅲ. 결론
다양한 장점과 응용 분야를 가지고 있는 마이크로 LED는 차세대 디스플레이로서 대만, 중국, 일본, 미국, 유럽이 상용화에 매진하고 있다. 마이크로 LED 상용화의 난제는 전사, 접합, 불량 화소 수리로서 이와 관련된 생산성을 높이고 비용을 줄이는 것이 절실하다. 이를 위해 본고에서는 소재를 중심으로 한 기술 개발 동향을 살펴보았다. 한국전자통신연구원이 개발한 동시 전사 접합 기술, SITRAB 기술은 마이크로 LED 상용화에 필요한 문제점들을 해결할 수 있는 장점이 있으며, 이와 같은 기술 개발은 17년이라는 장기간에 걸친 소재 기술 개발에 그 뿌리가 있다.
용어해설
인터포저(Interposer) ‘둘 사이에 놓다’라는 의미의 라틴어인 interpōnere에서 유래함. 전자 패키징에서는 다음과 같은 개념으로 사용됨. 두 개의 서로 다른 연결을 이어주는 전기적인 인터페이스 라우팅을 의미하며 ball grid array 패키지에서 IC와 솔더 볼(Solder Ball) 사이의 패키지 기판이 한 예. 마이크로 LED에서는 웨이퍼에서 제조된 마이크로 LED는 그 배열이 디스플레이 패널의 배열과는 다름. 이와 같은 문제를 해결하기 위해 인터포저상에 마이크로 LED를 디스플레이 패널 배열과 동일하게 배열함
약어 정리
ACF
Anisotropic Conductive Film
AR
Augmented Reality
HBM
High Bandwidth Memory
LAB
Laser-Assisted Bonding
LCD
Liquid Crystal Display
LED
Light Emitting DiodeAutomated Model Compression
NCF
Non-Conductive Film
NCP
Non-Conductive Paste
OLED
Organic Light-Emitting Diode
PDMS
Polydimethylsiloxane
SITRAB
Simultaneous Transfer and Bonding
VR
Virtual Reality
E.H. Virery et al., "MicroLED display technology trends and intellectual property landscape," SID 2020 Digest, vol. 51, no. 1, 2020, pp. 436-439.
E.H. Virery et al., "From lab to fab: Challenges and requirements for high-volume MicroLED manufacturing equipment," SID 2021 Digest, vol. 52, no. 1, 2021, pp. 826-829.
H. Lee et al., "Sn58Bi solder interconnection for low-temperature flex-on-flex bonding," ETRI J., vol. 38, no. 6, 2016, pp. 1163-1171.
K.-S. Choi et al., "Simultaneous transfer and bonding (SITRAB) process for Micro-LEDs using laser-assisted bonding with compression (LABC) process and SITRAB adhesive," in Proc. IEEE Electron. Compon. Technol. Conf., (San Diego, CA, USA), June 2021, pp. 1607-1613.
M. Nishida et al., "Laser lift off and multi dies collective bonding for inorganic μLED with the newly developed material," in Proc. IEEE Electron. Compon. Technol. Conf., (San Diego, CA, USA), June 2021, pp. 1916-1921.
K.-S. Choi et al., "Simultaneous transfer and bonding (SITRAB) process for Mini-LED display," SID 2021 Digest, vol. 52, no. 1, 2021, pp. 841-844.
J. Joo et al., "Development of simultaneous transferring and bonding (SITRAB) process for μLED arrays using anisotropic solder paste (ASP) and laser-assisted bonding (LAB) technology," in Proc. IEEE Electron. Compon. Technol. Conf., (San Diego, CA, USA), June 2021, pp. 687-692.
J. Joo et al., "Development of flexible full-color MiniLED display using simultaneous transfer and bonding (SITRAB) technology," SID Display Week, 2022, Accepted.
C.A. Bower et al., "Mass transfer throughput and yield using elastomer stamps," SID 2021 Digest, vol. 52, no. 1, 2021, pp. 849-852.
K.-S. Choi et al., "Enhanced performance of laser-assisted bonding with compression (LABC) compared with thermal compression bonding (TCB) technology," in Proc. IEEE Electron. Compon. Technol. Conf., (Las Vegas, NV, USA), May 2019, pp. 197-203.
K.-S. Choi et al., "Interconnection process using laser and hybrid underfill for LED array module on PET substrate," in Proc. IEEE Electron. Compon. Technol. Conf., (San Diego, CA, USA), May 2018, pp. 1567-1573.
W.A. Braganca et al., "Collective laser-assisted bonding process for 3D TSV integration with NCP," ETRI J., vol. 41, no. 3, 2019, pp. 396-407.
W.A. Braganca et al., "Silica filler content in NCP and its effects on the reliability of 3D TSV Multi-Stack under thermal shock test," in Proc. IEEE Electron. Packag. Technol. Conf. (EPTC), (Singapore, Singapore), Dec. 2017, pp. 1-8.
K.-S. Choi et al., "Development of stacking process for 3D TSV (through silicon via) structure using laser," Int. Symp. Microelectron., vo. 2017, no. 1, 2017, pp. 67-71.
K.-S. Choi et al., "Development of digital signage modules composed of Mini-LEDs using laser-assisted bonding (LAB) technology," in Proc. IEEE Electron. Compon. Technol. Conf., (Orlando, FL, USA), June 2020, pp. 1031-1036.
- Sign Up
- 전자통신동향분석 이메일 전자저널 구독을 원하시는 경우 정확한 이메일 주소를 입력하시기 바랍니다.