반도체 및 전자패키지의 방열기술 동향
Heat Dissipation Trends in Semiconductors and Electronic Packaging
- 저자
-
문석환저탄소집적기술창의연구실 shmoon@etri.re.kr 최광성저탄소집적기술창의연구실 kschoi@etri.re.kr 엄용성저탄소집적기술창의연구실 yseom@etri.re.kr 윤호경저탄소집적기술창의연구실 yunhg@etri.re.kr 주지호저탄소집적기술창의연구실 jihojoo@etri.re.kr 최광문저탄소집적기술창의연구실 gmchoi@etri.re.kr 신정호저탄소집적기술창의연구실 sjh0759@etri.re.kr
- 권호
- 38권 6호 (통권 205)
- 논문구분
- 사람 중심 인공지능과 미래 반도체 기술
- 페이지
- 41-51
- 발행일자
- 2023.12.01
- DOI
- 10.22648/ETRI.2023.J.380605
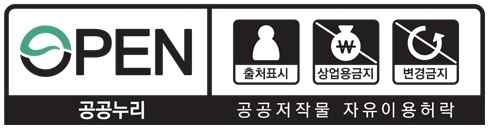
- 초록
- Heat dissipation technology for semiconductors and electronic packaging has a substantial impact on performance and lifespan, but efficient heat dissipation is currently facing limited improvement. Owing to the high integration density in electronic packaging, heat dissipation components must become thinner and increase their performance. Therefore, heat dissipation materials are being devised considering conductive heat transfer, carbon-based directional thermal conductivity improvements, functional heat dissipation composite materials with added fillers, and liquid-metal thermal interface materials. Additionally, in heat dissipation structure design, 3D printing-based complex heat dissipation fins, packages that expand the heat dissipation area, chip embedded structures that minimize contact thermal resistance, differential scanning calorimetry structures, and through-silicon-via technologies and their replacement technologies are being actively developed. Regarding dry cooling using single-phase and phase-change heat transfer, technologies for improving the vapor chamber performance and structural diversification are being investigated along with the miniaturization of heat pipes and high-performance capillary wicks. Meanwhile, in wet cooling with high heat flux, technologies for designing and manufacturing miniaturized flow paths, heat dissipating materials within flow paths, increasing heat dissipation area, and reducing pressure drops are being developed. We also analyze the development of direct cooling and immersion cooling technologies, which are gradually expanding to achieve near-junction cooling.
Share
Ⅰ. 서론
반도체 칩이 들어가는 스마트폰을 비롯한 대부분의 전자통신 기기들은 발열로 인한 성능 저하 및 수명 감소의 문제에 직면하고 있다. 저전력 설계 및 소프트웨어적 열관리를 하더라도 계속 증가하고 있는 칩의 고성능화는 열유속(Heat Flux)을 가속화하고 있는 실정이다. 특히 통신 속도의 증가 및 인공지능 기술의 발달로 더욱 강력한 열소산(Heat Dissipation) 수단이 요구되고 있으나, 열소산 수단의 크기 제약 및 기술적 대응 어려움은 점차 방열기술의 개발 한계에 봉착하고 있음을 실감케 한다[1]. 반도체 칩의 발생 열은 열전도도(Thermal Conductivity)가 높은 기판을 통해 1차적으로 소산(Dissipation)되며, 이어 패키지 레벨의 모듈로 전달돼 시스템 또는 주변으로 소산되는 열경로 과정을 따르게 된다. 상대적으로 방열면적 및 체적이 큰 모듈과 시스템에서는 조건 및 요구에 따라 다양한 열소산 수단을 적용할 수가 있어 지금까지 효과적으로 잘 대응할 수 있었다. 그러나 반도체 칩에서의 열점(Hot Spot)은 상대적으로 높은 열유속(Heat Flux)을 갖게 돼 적용할 수 있는 열소산 수단에 큰 제약을 받고 있다[2]. 즉, 칩의 크기에 따라 차이는 있을 수 있지만 칩에서의 발생 열을 직접 제어하기 위한 면적과 공간이 매우 협소해서 열소산을 위한 열흐름 경로를 효과적으로 마련하는 것이 쉽지 않다. 그럼에도 반도체 칩에서의 발생 열을 최대한 빠르게 소산시킬 수 있는 방열기술은 계속해서 발전할 필요가 있으며, 이는 시스템의 전체 열저항(Thermal Resistance) 중 반도체 칩의 접합 경계에서의 열저항이 가장 크게 나타나고 있기 때문이다. 그림 1은 냉각판(Cold Plate), CuW, 인터포저(Interposer)로 이루어진 패키지 모듈에 반도체 칩을 본딩한 경우에서의 접합구간별 열저항을 도시한 것이며, 실험결과에서도 볼 수 있듯이 반도체 칩의 정션(Junction)과 인터포저 간의 결합 계면에서의 열저항이 전체 열저항의 76%에 이를 정도로 가장 크게 나타나고 있음을 알 수 있다. 따라서 전자패키지 분야에서 모듈 및 시스템 관련 방열기술이 상대적으로 더욱 많은 발전을 이루어 온 점을 고려했을 때, 앞으로는 반도체 칩에서의 효과적 방열을 위한 정션 근접(Near Junction) 방열기술의 발전을 위한 설계 및 수단의 개발이 뒤따라야 할 것으로 생각한다[3]. 본고에서는 반도체 칩을 포함한 전자패키지에서의 방열 기술 개발 동향을 분석하고자 하였으며, 크게 전도(Conduction) 열전달 방식의 방열기술과 단상(Single Phase) 및 상변화(Phase Change) 기반 방열기술로 구분해 서술하고자 한다.
Ⅱ. 전도 열전달 방식의 방열기술
1. 방열소재 기술 개발 동향
고상(Solid Phase)의 소재를 통한 전도 열전달 및 열소산이 전자패키지에서는 기본적인 열방출 통로로 이용된다. 반도체 소자 및 패키지에 적용되는 대부분 부품은 열팽창계수 등의 신뢰성을 고려함과 동시에 방열성능 확보를 위한 높은 열전도도 특성이 요구되고 있다. 세라믹, 금속 및 이들의 합금을 제외하고 카본 소재가 갖는 열전도도는 상대적으로 매우 크기 때문에 전도 열전달 방식의 방열수단으로 자주 고려되고 있다. California University에서는 그라핀(Grahpene)을 열 스프레더(Heat Spreader)로 활용하기 위한 방열구조를 개발한 바 있으며, 다수 개의 층(Layer)으로 적층해 수평 방향(In-plane)의 열전달량을 증가시키고자 하였다. 연구 결과를 통해서는 12.8W/mm의 전력 밀도하에서 전력 반도체 소자의 온도를 약 20℃가량 감소시킬 수 있는 것으로 보고되었다. 얇은 그라핀 층들을 다루는 것이 쉽지는 않겠지만, 카본 소재는 잘 알려진 바와 같이 전도 열전달 방열수단으로써 매우 우수한 잠재력을 가진다고 볼 수 있다. 그러한 측면에서 전자패키지에서 접착제(Paste)로 많이 사용하는 에폭시의 열전도도를 향상시키기 위한 노력이 지난 수십 년간 꾸준하게 지속되어 왔다. 그림 2는 대표적으로 기존 에폭시 레진에 카본 열전도성 필러(Filler)를 혼합해 열전도도를 향상시킨 연구 결과를 보여주고 있다. 순수 에폭시 대비 약 225%의 열전도도 증가 특성을 얻을 수 있었던 것으로 보고되었으며, 이러한 기능성 복합 소재의 개발은 근래 들어 증가하는 추세이다.
고열전달을 위한 또 다른 방열소재로 소결(Sintering) 방식의 접착제가 제시되었으며, 당초 은(Ag) 소결 접착제에서 저가화를 위한 구리(Cu) 소결 접착제로의 전환을 위한 연구가 근래 진행되고 있다. 그림 3은 나노(Nano) 구리 소결 접착제 개발 결과이며, 기존 은(Ag) 소결 접착제와 특성은 비슷하면서 제조 비용을 낮출 수 있는 것으로 보고되고 있다.
부품을 장착할 때 방열을 위한 계면 접착제를 TIM(Thermal Interface Material)이라 하며, 대표적으로 Grease, PAD, PCM(Phase Change Material) 등이 주로 사용된다. 이러한 기존 실리콘, 폴리머 소재 기반 TIM을 열전도도가 높은 액체 금속으로 대체함으로써 열소산 경로에서 가장 큰 열저항을 갖는 접합 계면을 개선하고자 하는 연구가 보고되고 있으며, 다만 칩 선단(Edge)에서의 박리(Delamination) 현상 해결은 뒤따라야 할 것으로 파악된다[6]. 이에 한발 더 나아가 고상의 TIM 대신 상온 액상(Liquid Phase)의 TIM을 사용함으로써 기존 TIM이 갖는 스트레스(Stress), 박리 및 열저항의 문제점을 해결하려는 기술 개발 또한 보고되고 있다[7].
방열 성능을 향상시키려는 노력의 일환으로 복합 소재화하는 기술은 접착제뿐만 아니라 필름 및 기판 형태로도 개발해 열 스프레더(Heat Spreader)로 활용될 수 있다. 관련해 ETRI에서는 그림 4와 같이 카본 그라파이트(Graphite)를 기본 소재로 하면서 via 형태의 filler를 첨가해 수평뿐만 아니라 수직 열전도도까지 향상시키고, TPU 소재를 라미네이팅(Laminating)해 내충격 기능까지 추가한 방열 복합소재 시트를 개발해오고 있다.
2. 방열구조 기술 개발 동향
앞 절에서 방열소재 기술에 대해 살펴봤다면, 이 절에서는 열소산을 극대화하기 위한 방열구조의 설계 및 제작에 관한 기술 개발 동향을 요약하고자 한다. 전자기기에서 방출되는 열은 전도 열전달을 통해 공기 또는 액체로 소산되며, 이때 가장 기본적인 방열 솔루션이 히트싱크(Heat Sink)이다. 히트싱크는 오래된 기술이면서 가장 많이 사용되고 있으며, 전자패키지에서는 방열면적 증가뿐만 아니라 대류열 전달계수(Convection Heat Transfer Coefficient)를 향상시키기 위한 기술 개발이 진행돼 오고 있다. 향후 스마트폰을 비롯해 좁은 전자패키지 공간에서의 히트 싱크 초소형화 요구는 증가할 것으로 예상되며, 그러한 측면에서 그림 5와 같이 금속이온이 용해된 액체 내에서 이동하고, 구조물 형성을 위해 원하는 위치에 증착될 수 있는 기술 개발이 근래 보고되었다.
반도체 칩의 패키징 구조는 방열 설계에 따라 열소산 효과에 큰 차이를 보이며, 우선적으로 방열을 위한 접촉면적을 최대한 확보하는 것이 관건이다. 그림 6은 그러한 측면에서 컵(Cup)형의 구리 방열 패키징 구조물을 보여주고 있으며, 솔더(Solder) 및 메탈PCB(MPCB)의 방열 도움 외에 컵형에 의해 방열면적을 2배로 늘리는 효과를 얻을 수 있게 된다. 한편 방열면적과 대류열전달계수의 확보를 위한 히트싱크는 일반적으로 발열 부품에 부착하는 형태로 적용되나, 칩 및 발열소자를 히트싱크에 직접 삽입하는 구조로 개발된다면 계면 열저항을 줄일 수 있어 방열성능에 유리할 수 있다. 그러한 측면에서 SiC 칩을 전기주조법(Electroforming)으로 제작된 히트싱크에 삽입하는 패키지 구조가 개발된 바 있으며, 기존 구조 대비 열소산량을 약 1.6배가량 향상시킬 수 있는 것으로 보고되고 있다.
한편, 발열 밀도가 큰 전력반도체 전자패키지의 경우 단측면(Single Side) 냉각판(Cold Plate)을 이용해 열을 방출해 왔으며, 근래 들어서는 양측면(Double Side)으로까지 냉각판을 설치하는 구조 설계가 이루어진다. 그림 7은 그러한 양측면 냉각판 사이에 전자패키지 구조를 장착하고, 이때 리드프레임(Lead Frame)으로 두껍고 넓은 폭의 구리 클립(Cu clip)을 사용함으로써 방열 통로(Path)를 크게 확보할 수 있도록 개발한 구조를 보여주고 있다.
열유속 증가뿐만 아니라 패키징 밀도 또한 점차 증가하게 되면, 3차원 적층 구조로의 설계가 적극 고려될 수 있을 것이다. 2차원에서의 방열 설계와 달리 3차원 구조에서는 적용할 수 있는 방열 솔루션이 극히 제한적인 실정이다. 그림 8은 그러한 측면에서 TSV(Through Silicon Via) 적용을 통해 열적 특성이 취약한 논리 적층 패키지 구조(Logic Stack Pakage Structure)를 갖는 에스램(SRAM)에서 마이크로 범프 정션(Micro Bump Junction)의 열저항을 감소시키고자한 구조 제시이다.
그러나, TSV는 제작의 어려움에 더해 공정 비용 또한 고가임에 따라, 이를 대체하고자 하는 기술 개발이 진행되고 있다. 그림 9는 다층으로 구성된 BEOL(Back End of the Line) 배선공정을 통해 TSV 대체 가능성을 제시한 기술에 해당한다.
Ⅲ. 단상 및 상변화 기반 방열기술
1. 건식 형 방열기술
앞 절에서 살펴본 방열소재 및 방열구조의 기술로 감당하기 어려워지는 고열유속은 단상 및 상변화 방식의 열전달 수단으로 해결할 수 있다. 노트북을 포함한 소형 전자기기에 히트파이프 기술이 적용되기 시작한 것은 오래되지 않았으며, 약 2000년대 초반부터이다. 아울러 스마트폰에 소형 히트파이프 기술이 적용된 것은 2016년이 처음이다[1]. 그만큼 전자기기 내 발열 열유속은 가파르게 증가하고 있다. 히트파이프는 냉각액을 사용하는 습식에 비해 완전 밀폐된 용기(Envelope) 내에 작동유체(Working Fluid)가 충진(Filling)되어 있어 건식(Dry Type) 솔루션에 해당한다. 히트파이프는 상변화(Phase Change)에 의한 잠열(Latent Heat)을 이용하기 때문에 많은 열을, 또한 내부가 진공(Vacuum)이기 때문에 빠르게 열을 전달할 수 있으며, 구조가 단순하고 다양한 형태로 설계가 가능해 그 용도는 매우 넓다. 다만, 산업용으로 사용되는 큰 직경의 히트파이프와 달리, 전자패키지 분야에서는 미니(Mini) 또는 마이크로(Micro) 히트파이프 크기의 기술이 적합하다. 이러한 마이크로 히트파이프는 크기가 작고 가격도 저렴할 수 있지만, 제조기술은 훨씬 어려운 단점을 안고 있다. 환상(Circular) 또는 다각 단면 파이프형 마이크로 히트파이프를 별도로 제작하고 이를 패키징에 적합한 형상으로 2차 가공해 적용하는 경우가 많으며, 웨이퍼 또는 기판을 식각해 마이크로 히트파이프를 제작하는 임베디드(Embedded)형의 기술도 개발되고 있다. 그림 10은 마이크로 히트파이프의 작동원리 및 구조를 나타낸 것이다. 전자의 경우는 이미 상용화가 이루어진 반면, 후자의 경우는 개발 취지에 비해 아직 기술적 난관에 봉착해 있다. 이는 실리콘 웨이퍼 또는 기판에 가공하는 형태는 기술적으로 어려울 뿐만 아니라 마이크로 히트파이프는 내부 작동유체 기체-액체(Vapor-Liquid) 계면에서의 마찰저항에 의한 압력강하(Pressure Drop)를 줄이고, 이를 보완할 수 있는 고성능의 미세 모세관 윅(Capillary Wick)의 개발이 요구되기 때문이다. ETRI에서는 25년 이상 마이크로 히트파이프 기술을 개발해왔으며, 특히 알루미늄(Aluminum) 소재 기반의 판상형 다채널 히트파이프를 2000년대 초에 개발해 원천특허 보유 및 상업화와 더불어 기술 향상을 계속해서 추진해 오고 있다. 그림 11은 ETRI에서 개발한 AFHP(Aluminum Flat Heat Pipe)의 외형 및 단면 구조를 보여주고 있다.
ETRI에서 개발한 AFHP 기술은 기존 구리 소재 기반의 히트파이프를 무게가 1/3로 가벼운 알루미늄으로 전환하고, 저가화 공정 및 다채널 또는 채널 분리형 등의 장점을 기반으로 기존 구리 히트파이프가 가지지 못한 설계의 다양성을 갖출 수 있게 되었다. 무엇보다 중요한 장점은 환상 형 구리 히트파이프를 패키지하기 위해서는 압착하여 사용하는데, 압착할 수 있는 폭(Width)에 한계가 있어 대면적화가 어려운 반면, ETRI의 AFHP는 200mm 이상의 판상화가 가능하다는 데 있다.
최근에는 그림 12와 같이 카본 와이어 다발(Carbon Wire Bundle)을 이용한 미세 모세관 복합 윅을 개발한 바 있다.
히트파이프와 작동원리는 동일하나 열스프레딩(Heat Spreading)의 목적으로 증기챔버(Vapor Chamber) 기술이 근래 상품화되어 휴대기기를 중심으로 많이 적용 중이다. 증기챔버는 환상형 히트파이프와 달리 판상형이면서 상대적으로 넓은 면적을 갖도록 설계되며, 면상 내에서 열점(Hot Spot) 제거와 열소산이 되도록 작동한다. 상변화 열전달 작동은 넓은 양쪽 면이 각각 증발부(Evaporator)와 응축부(Condenser) 역할을 하면서 이루어지며, 내부 진공에 따른 함몰 현상 방지와 응축액의 유동 통로로 이용하기 위한 기둥(Column)이 중간에 다수 개 설치되는 특징을 갖는다. 물론 설계에 따라서는 이와 같은 기둥이 다양한 형태로 설계될 수도 있다. 증기챔버는 당초 목적이 면상 발열체 내 열점 제거와 함께 온도 편차를 최소화하는 목적을 지녔으나, 근래에는 면상에서의 열소산 기능에 더욱 치우치는 경향을 보이는 것으로 분석된다. 그림 13은 증기챔버의 작동 원리 패키지에 적용을 위한 개략도를 보여주고 있다. 증기챔버의 활용에 있어 히트파이프도 마찬가지지만, 목적에 따라 형태 및 설계가 적합하게 이루어져야 하는 점이 중요하다.
또한, 직경이 작은 히트파이프에서와 마찬가지로 두께가 얇은 증기챔버의 경우, 작동성능을 확보하기 위해서는 내부 작동유체의 압력강하를 극복하기 위한 고성능의 모세관 윅을 확보하는 것이 중요하다. 그러한 측면에서 그림 14는 구리 폼(Foam) 위에 그라핀을 증착해 성긴 윅(Coarse Wick)과 미세 윅(Fine Wick)을 동시에 가질 수 있도록 복합 모세관 윅을 개발한 예이다. 모세관 윅은 작동액의 유동량과 모세관력이 최적으로 확보될 수 있도록 개발하는 점이 중요하다.
2. 습식형 방열기술
열을 소산시키는 히트싱크 역할은 유체(Fluid)가 담당하며, 비체적이 큰 공기에 비해 액체는 가장 많은 열유속을 해결할 수 있는 방열수단이다. 액체냉각(Liquid Cooling)은 그동안 주로 산업 분야에서 열교환기(Heat Exchanger), 냉각탑 등에서 사용되어 왔으나, 전자패키지 분야에서는 누수(Water Leak) 및 크기 등의 문제로 고려되지 않아 왔다. 그러나 서버를 비롯한 전자패키지 분야에서 점차 열유속이 크게 증가하면서 오픈형 액체냉각뿐만 아니라 독립 밀폐형 액체냉각 기술까지 개발이 이루어지고 있다.
전자패키지에 적용하는 액체냉각 기술은 그림 15와 같이 칩의 패키지 모듈에 덧붙이는 형태로 가장 간단하게 적용 가능하다. 즉, 칩에서의 발생 열은 패키지 모듈을 통해 전도(Conduction) 열전달되며, 이후 덧붙여진 액체냉각 모듈을 통해 방열되는 형태이다. 이러한 경우에서는 액체냉각 모듈의 방열성능이 우수하더라도 칩 패키지 모듈과의 접촉 열전달 면적에 한계가 있어, 근본적인 열소산량에 제약이 따를 수 있다.
공냉에서의 히트싱크처럼 액체냉각에서도 방열 면적을 증가시키기 위한 구조 설계가 뒤따라야 하며, 액체 유로에서의 압력강하를 최소화하면서 방열면적의 극대화를 이루고, 덧붙여 그림 16과 같이 고열전도도 소재의 채용 또한 적극적으로 고려할 필요가 있다. 여기서는 다이아몬드 기판(Substrate)뿐만 아니라 미세 Cu 기둥(Pillar)을 액체유로에 설치함으로써 열유속을 650W/cm2 까지 달성한 예를 보여주고 있다.
전자패키지에서 액체유로 제작 기술은 연구 단계에서는 고가의 반도체 공정을 이용하고 있으나, 상용화를 위해서는 저가 및 공정의 단순화를 달성할 필요가 있다. 그러한 측면에서 그림 17과 같이 기존 CVD(Chemical Vapor Deposition) 또는 MEMS(Micro Electro Mechanical System) 공정 대신 3D 프린팅 및 에칭(Etching) 공정으로 액체유로 내 히트싱크 구조를 제작할 수 있다. 특히 다수 개의 환상형 기둥이 액체유로 내 방열구조로 근래 많이 제시되고 있으며, 이는 방열면적, 압력강하 및 구조의 강건성(Robustness)을 고려한 것으로 볼 수 있다.
전자패키지 구조 내 열저항은 소자와 부품 간 결합 계면에서 크게 나타나며, 이를 감소시키기 위한 고열전도도 접합 소재의 선정과 더불어 적용 가능한 냉각 수단, 즉 열을 빼앗아 가는 선단(Edge)이 칩에 가까울수록 유리하다. 이는 근래 들어 정션 근처 냉각(Near Junction Cooling)이라는 개념으로 많이 연구되고 있다. 그림 18은 그러한 측면에서 전자패키지 모듈의 리드(Lid)를 없애고 냉각액체가 직접 발열칩에 접촉하도록 설계한 예이다.
한편, 그림 18에서의 직접냉각(Direct Cooling)처럼 냉각액을 발열소자에 직접 분사하는 패키지 구조를 설계할 수도 있으며, 이를 분사냉각(Spray Cooling)이라 한다. 다이(Die)의 뒤틀림(Warpage) 현상 방지를 위해 뒷면(Backside)에 분사냉각 방법을 적용할 수 있다.
그러나, 열유속이 매우 크고 열점의 위치가 복잡한 경우에 적용할 수 있는 방열수단은 제한적이게 되므로, 이때 액침냉각(Immersion Cooling)을 고려해 볼 수 있다. 액침냉각은 발열부 전체가 냉각액 내에 담기게 돼 가장 효과적인 방열수단이 될 수 있는 반면, 시스템의 안전성 및 신뢰성 그리고 유지 관리의 어려움은 상용화를 주저하게 한다. 그림 19와 같이 반도체 패키지 구조 내 오픈의 용기 형태로 설계해 제작할 수도 있다.
이러한 경우 개별 패키지 모듈마다 액침냉각 기술을 적용해야 하는 단점은 안고 있지만, 5G 이상의 고속 계산용 반도체 칩처럼 상대적으로 크기가 크고, 시스템 내 주요 열점에 해당한다면 바람직한 열소산 수단이 될 수 있다. 랙(Rack)에 다수 개의 서버(Server)가 설치되는 경우, 액침냉각을 서버 레벨에서의 적용을 고려해 볼 수도 있다. 이러한 경우 앞선 패키지 모듈 레벨에 비해 방열 효율 및 열점의 온도 제어가 훨씬 쉬워질 수 있다. 한발 더 나아가 데이터 센터와 같이 대형 공간에 다수 대의 서버 랙이 들어 차 있는 경우에까지 액침냉각이 적용된다면, 기존 데이터센터 공간의 획기적인 축소, 방열효율의 획기적 증가, IT전력 대비 냉방전력의 획기적 감소를 통해 PUE(Power Usage Effectiveness) 1.5 미만의 고집적 데이터센터의 구현도 기대해 볼 수 있을 것이다. 액침냉각의 칩 레벨 방열 효율의 향상을 위한 기술 개발은 가장 근간이 되는 연구이며, 그림 20과 같이 패키지 리드에 비등열전달(Boiling Heat Transfer) 촉진 기술 접목을 통해 대류열전달계수(Convection Heat Transfer Coefficient)를 극대화시키는 방법 등이 좋은 예가 될 수 있다.
Ⅳ. 결론
반도체 및 전자패키지의 방열기술은 얇고 부피가 작으면서 고성능화가 요구되고 있다. 칩 근처에까지 방열수단을 적용함으로써 열점을 해결하고자 하며, 이를 위한 고열전도도의 방열 복합소재, 3D 프린팅 기반 복잡한 방열구조 기술 등이 개발되고 있다. 히트파이프 및 증기챔버 기술 또한 가볍고 얇으면서 고성능화를 위한 발전을 거듭하고 있다. 전자 통신 기기의 열유속이 점차 증가하고 있어, 단상 및 다상 유동의 액체냉각 및 액침냉각 기술들이 더욱 구체화되고 있는 것으로 분석된다. 향후 고속 계산이 요구되는 서버 등에서는 높은 열유속 해결이 가능하고, 낮은 작동온도 유지 및 적은 전력소모를 지향하고, 더 나아가 수요가 점차 늘어날 것으로 보이는 데이터센터의 냉방전력 또한 획기적 감소를 통한 저탄소 기술 실현이 요구될 것으로 보인다.
용어해설
Heat Pipe 금속 소재 용기(Envelope) 내에 작동유체(Working Fluid)가 주입되며, 기체-액체 상변화에 의해 잠열 형태의 흡열 및 방열이 이루어짐. 내부에 모세관 윅이 설치되며, 진공밀폐 구조를 갖는 방열소자임
Vapor Chamber 히트파이프와 작동원리는 유사하며, 히트파이프가 대부분 환상(Circular) 형임에 비해, 증기챔버는 판상(Flat Plate) 형을 띰. 주로 평판 내 열점(Hot Spot) 제거 및 온도 편차 감소의 기능을 가지나, 최근에는 방열수단으로 더 인식되고 있음
약어 정리
S.H. Moon et al., "Application of aluminum flat heat pipe for dry cooling near the hot spot of a radar array with a multiscale structure," Appl. Therm. Eng., vol. 169, 2020.
Z. Sun et al., "Large-scale and low-cost production of graphene nanosheets-based epoxy nanocomposites with latent catalyst to enhance thermal conductivity for electronic encapsulation," in Proc. ECTC, (San Diego, CA, USA), June 2021.
X. Liu et al., "Study and application of nano copper sintering technology in power electronics packaging," in Proc. ECTC, (San Diego, CA, USA), June 2021.
Y. Kim et al., "Metal thermal interface material for the next generation FCBGA," in Proc. ECTC, (San Diego, CA, USA), June 2021.
Y.L. Huang et al., "Highly thermal dissipation for large hpc package using liquid metal materials," in Proc. ECTC, (San Diego, CA, USA), June 2021.
M. Frank et al., "Electrochemical additive manufacturing: A novel approch to thermal management of electronics," in Proc. ECTC, (Orlando, FL, USA), May 2023.
R.H. Horng et al., "Optimized thermal management from a chip to a heat sink for high-power GaN-based light emitting diodes," IEEE Trans. Electron Devices, vol. 57, no. 9, 2010.
G. Tang et al., "Development of a novel lead frame based double side liquid cooling high performance SiC power module," in Proc. ECTC, (San Diego, CA, USA), June 2021.
S.K. Seo et al., "CoW package solution for improving thermal characteristic of TSV-SiP for AI-inference," in Proc. ECTC, (San Diego, CA, USA), June 2021.
K. Matsumoto et al., "Thermal analysis of DBHi (direct bonded heterogeneous integration) Si Bridge," in Proc. ECTC, (San Diego, CA, USA), June 2021.
R. Wong et al., "Copper-graphene foams: A new high-performance material system for advanced package-integrated cooling technologies," in Proc. ECTC, (San Diego, CA, USA), June 2021.
B. Lohani, S.D. Hossain, and R.C. Roberts, "Metal additively microfabricated sipswith embedded microfluidic cooling towards heterogeneous integration with SoCs," in Proc. ECTC, (Orlando, FL, USA), May 2023.
Z. Zhang et al., "A promising solution using CVD diamond for efficient cooling of power device," Mater. Sci. Eng. B, vol. 177, 2012, pp. 1358-1361.
S.K. Rajan et al., "Design considerations, demonstration, and benchmarking of silicon microcoldplate and monolithic microfluidic cooling for 2.5D ICs," in Proc. ECTC, (San Diego, CA, USA), June 2021.
J.N. Hung et al., "Advanced system integration for high performance computing with liquid cooling," in Proc. ECTC, (San Diego, CA, USA), June 2021.
G. Tang, L.C. Wai, and H. Feng, "Development and demonstration of a novel immersion two phase cooling high power sicpower module," in Proc. ECTC, (Orlando, FL, USA), May 2023.
- Sign Up
- 전자통신동향분석 이메일 전자저널 구독을 원하시는 경우 정확한 이메일 주소를 입력하시기 바랍니다.